ENERFLOW 880 NITROGEN PUMP
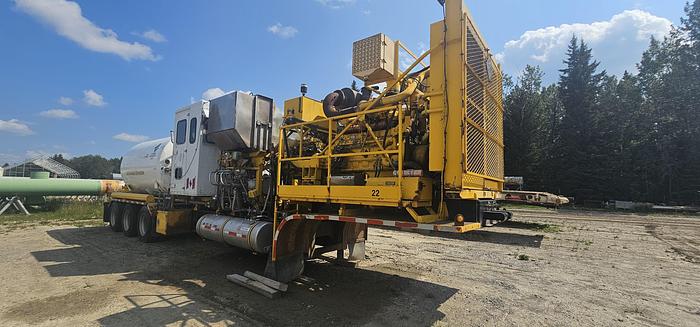
ENERFLOW 880 NITROGEN PUMP
Contact us for price
Description
2006 ENERFLOW NP300 ( MODEL )
- DIRECT FIRE UNIT
Serial : E051284A-134001
CHASSIS : 2PLC044397EF13122
45'5" Long
8'7" Wide
12' High
400 Cubic ft./ min
QFK 23 Cummins Engine VIN 00313738
1502 PIPING AND VALVES
8000 CUBE OF GAS
3800 GALLONS LIQUID
7,900hrs
RECERTIFIED TURN KEY
We belive this was the original spec when built : from NOV
This specification provides the minimum requirements for the design, description, fabrication and testing of a unit in this specification for a diesel fired nitrogen pump unit rated at 311.5 m3/min (11,000 scfm) maximum discharge rate and 68,950 kPa (10,000 psi)
This document was generated under the authority of Enerflow Industries Inc. for the purpose of specifying the design requirements for a pumping unit.
This specification will be recognized as an integral part of the procurement agreement. Enerflow Industries will abide by the information and conditions set forth by this document as well as the standard term and conditions.
The unit consists of a custom built pumping unit and liquid nitrogen storage tank mounted on a semi-trailer. The unit is equipped with a diesel engine coupled with an Allison power-shift transmission driving a high pressure, positive displacement cryogenic triplex pump. Nitrogen is vaporized through a direct-fired vaporizer constructed of stainless steel that utilizes heat generated by diesel fuel, with a propane pilot for initial ignition. A hydraulically driven fan forces air into the vaporizer for efficient combustion of fuel. This system is protected with a high temperature fuel cutout device. Liquid nitrogen is transported in a "thermos-type" vessel, at -196°C (-320°F), mounted on the rear of the chassis.
The operation of the unit is controlled and monitored from a control station located in the cab on the unit and with devices arranged to allow the operator to control pump rate, nitrogen discharge pressure and temperature, and to monitor all vital engine and pump functions.
2.1. Trailer
2.1.1. The semi-trailer chassis is a custom manufactured chassis
2.1.2.
Tridem axle air ride suspension with a 60 inch spread
2.1.3.
Aluminum wheels brushed
2.1.4.
Antilock brake system
2.1.5.
Rear tow lugs on the trailer frame
2.1.6. Wheelbase to be determined
2.2. Fuel Tank
2.2.1. Two 150 USG aluminum fuel tank. Note more fuel will be provided based upon final unit configuration.
2.3. Deck Engine
2.3.1.
The deck engine is a diesel engine rated to 950 bhp (nominal) at 2,100 rpm. Specifications are as follows:
2.3.2. Heavy duty air cleaners
2.3.3. Air compressor
2.3.4. Alternator 24VDC
2.3.5. High ambient radiator with variable speed blower fan
2.3.6.
Single w/muffler exhaust system
2.3.7. 24 VDC starter
2.3.8. Rigsaver style emergency shutdown system
2.3.9. Diesel fired engine pre-heater
2.4. Transmission
2.4.1. The Allison 8610 transmission delivers power through a speed reduction gearbox to the triplex pump. See specification as follows:
2.4.2. Hydraulic torque converter
2.4.3.
Single mode power-shift
2.4.4. 6 output speeds
2.4.5. Spicer output flange
2.4.6.
Pressure lubrication system with cooler
2.5. Vaporizer
2.5.1. The direct-fired nitrogen vaporizer system is fabricated from stainless steel and is rated to 311.5 m3/min (11,000 scf/min) at 68,950 kPa (10,000 psi).
2.5.2. Main fuel is diesel.
2.5.3. A hydraulically driven fan forces air into the vaporizer for efficient combustion of fuel.
2.5.4. This system is protected with a high temperature fuel cutout device.
2.6. Triplex Pump
2.6.1. The pump is an ACD 3-SLS 600 high pressure, positive displacement cryogenic triplex pump designed to pump liquid nitrogen.
2.6.2. Cold ends are individual and identical
2.6.3. Power end is separate
2.6.4. Stuffing box seals are TFE
2.6.5. Externally lubricated warm end
2.6.6. Stroke is 57.2 mm (2.25 inch)
2.6.7. Cold end diameter is 64 mm (2.7 inch) cold ends for a maximum discharge pressure of 10,000 psi
2.7. Boost Pump
2.7.1. The boost pump is a close coupled 50.8 mm x 76.2 mm x 152 mm (2 inch x 3 inch x 6 inch) centrifugal pump that is hydraulically driven and delivers liquid nitrogen to the triplex pump or selectively returns liquid nitrogen to the tank.
2.7.2. A liquid nitrogen strainer is installed between the centrifugal pump and the triplex pump with gauges located on the upstream and downstream sides.
2.8. Suction Piping
2.8.1. Low pressure suction piping is arranged with appropriate valving to allow the triplex pump to be cooled down prior to operation, and to deliver pressurized liquid nitrogen from the trailer mounted tank using a hydraulically driven cryogenic centrifugal pump. The liquid nitrogen may be selectively re-circulated to the tank or delivered to the triplex pump depending on valve positioning.
2.8.2. Piping is also arranged to permit simultaneous transfer of liquid nitrogen from a bulk unit during pumping operations. The tank-loading manifold permits load hoses to be connected from either side of the unit or from the rear of the tank.
2.9. Discharge Piping
2.9.1. All high pressure nitrogen flow lines to include medium pressure fittings in conjunction with 2" Figure 1502 components.
2.9.2. All nitrogen lines are to be routed as per the P&ID.
2.9.3. The discharge line is equipped with a high- pressure cryogenic relief valve (set at 72.4 MPa (10,500 psi)) to prevent over pressure conditions.
2.9.4. The gaseous nitrogen is delivered from the vaporizer through a combination of stainless steel tubing and 50.8 mm (2 inch) Figure 1502 components which is equipped with a check valve, thermocouple, tee (pressure gauge connection) and a 50.8 mm (2 inch) Figure 1502 female (wing half) union outlet to the rear of the unit where the treatment line connection is made.
2.10. Nitrogen Storage Tank
2.10.1. 3000 USG nominal capacity
2.10.2. Double walled, vacuum insulated.
2.10.3. Inner tank configuration to be cylindrical in a horizontal plane.
2.10.4. Net capacity dependent upon weight allowance.
2.10.5. Maximum allowable working pressure to be approximately 40 psig.
2.10.6. Service temperature to be -320° F.
2.10.7. Super Insulation.
2.10.8. The tank may also be selectively loaded from the top or the bottom.
2.10.9. Normal Evaporation Rate to be less than 1% of total tank volume per day.
2.10.10. Tank width to be 8'6" or less.
2.10.11. Tank design should meet Compressed Gas Association specifications from pamphlet #341 entitled "Insulated Tank Truck Specification for Cold, Liquefied Gases".
2.10.12. Tank design should meet Section VIII Division 1, ASME Boiler and Pressure Vessel Code.
2.10.13. Inner vessel shall be designed, fabricated, and tested in accordance with Section VIII, Division I, ASME Boiler and Pressure Vessel Code.
2.10.14. Vessel should be stamped to indicated compliance.
2.10.19. A place for a high vacuum thermocouple gauge tube should be installed to permit periodic vacuum monitoring.
2.10.20. The internal to external plumbing should accommodate at minimum, 3 inch liquid outlet for pump, pressure gauge/liquid level gauge, top and bottom fill, pressure relief, and liquid/gas return from pumps. Pressure relief piping will include main relief, road relief valve, vent and rupture disc.
2.11. Hydraulic System
2.11.1. The centrifugal cryogenic boost pump, cab air conditioning, triplex lube oil pump, vaporizer fuel pump and the vaporizer blower are all hydraulically driven.
2.11.2. The hydraulic pumps are all driven from the deck engine
2.11.3. The hydraulic reservoir is equipped with a temperature / sight level gauge, suction screen, return filter and clean out cover
2.11.4. Main discharge valve includes a hydraulic actuation system
3. Chassis Control Cabin
3.1.1. The control console within the cabin includes engraved faceplates for all of the controls and instrumentation
3.1.2. Rear and side window
3.1.3. Cab constructed of aluminum
3.1.4. Heater and air conditioner
3.1.5. Interior lighting
3. Chassis Control Cabin
3.1.1. The control console within the cabin includes engraved faceplates for all of the controls and instrumentation
3.1.2. Rear and side window
3.1.3. Cab constructed of aluminum
3.1.4. Heater and air conditioner
3.1.5. Interior lighting
4. Controls and Instrumentation
All controls will be operated from a remote control with the exception of process control valves which will be via manual handles.
4.1.1. Enerflow ECAMSTM control system
4.1.2. Engine tachometer
4.1.3. Engine hour meter display
4.1.4. Engine Off/On/Start switch
4.1.5. Engine oil pressure display
4.1.6. Engine temperature display
4.1.7. Emergency air intake shutdown (Rigsaver style)
4.1.8. Transmission temperature display
4.1.9. Transmission lube oil pressure display
4.1.10. Transmission lock up/converter mode display
4.1.11. Transmission current gear select display
4.1.12. Speed control for LN2 boost pump with automatic or manual control
4.1.13. LN2 boost pump discharge pressure display
4.1.14. Triplex lube oil temperature display
4.1.15. Triplex lube oil pressure display
4.1.16. LN2 discharge pressure display
4.1.17. GN2 discharge pressure display
4.1.18. GN2 discharge flow rate and total display that is pressure and temperature compensated
4.1.1. Enerflow ECAMSIM control system
4.1.2. Engine tachometer
4.1.3. Engine hour meter display
4.1.4. Engine Off/On/Start switch
4.1.5. Engine oil pressure display
4.1.6. Engine temperature display
4.1.7. Emergency air intake shutdown (Rigsaver style)
4.1.8. Transmission temperature display
4.1.9. Transmission lube oil pressure display
4.1.10. Transmission lock up/converter mode display
4.1.11. Transmission current gear select display
4.1.12. Speed control for LN2 boost pump with automatic or manual control
4.1.13. LN2 boost pump discharge pressure display
4.1.14. Triplex lube oil temperature display
4.1.15. Triplex lube oil pressure display
4.1.16. LN2 discharge pressure display
4.1.17. GN2 discharge pressure display
4.1.18. GN2 discharge flow rate and total display that is pressure and temperature compensated
4.1.19. Over-pressure shutdown
4.1.20. GN2 discharge temperature automated control
4.1.21. LN2 tank gauges are located on the nitrogen tank
4.1.22. "ECAMS Digital Dashboard" software
4.1.23. "ICONICS" software
4.1.24. "ΙΝAT OPC Server" software
4.1.25. Optional data recording requires a separate computer. See Enerflow for detailed specifications for this computer.
Specifications
Manufacturer | ENERFLOW |
Model | NP300 NITROGEN PUMP |
Year | 2006 |
Condition | Used |
Serial Number | 2PLC044397EF13122 |
Stock Number | EF13122 |